Learn how IoT is helping cold storage warehouses
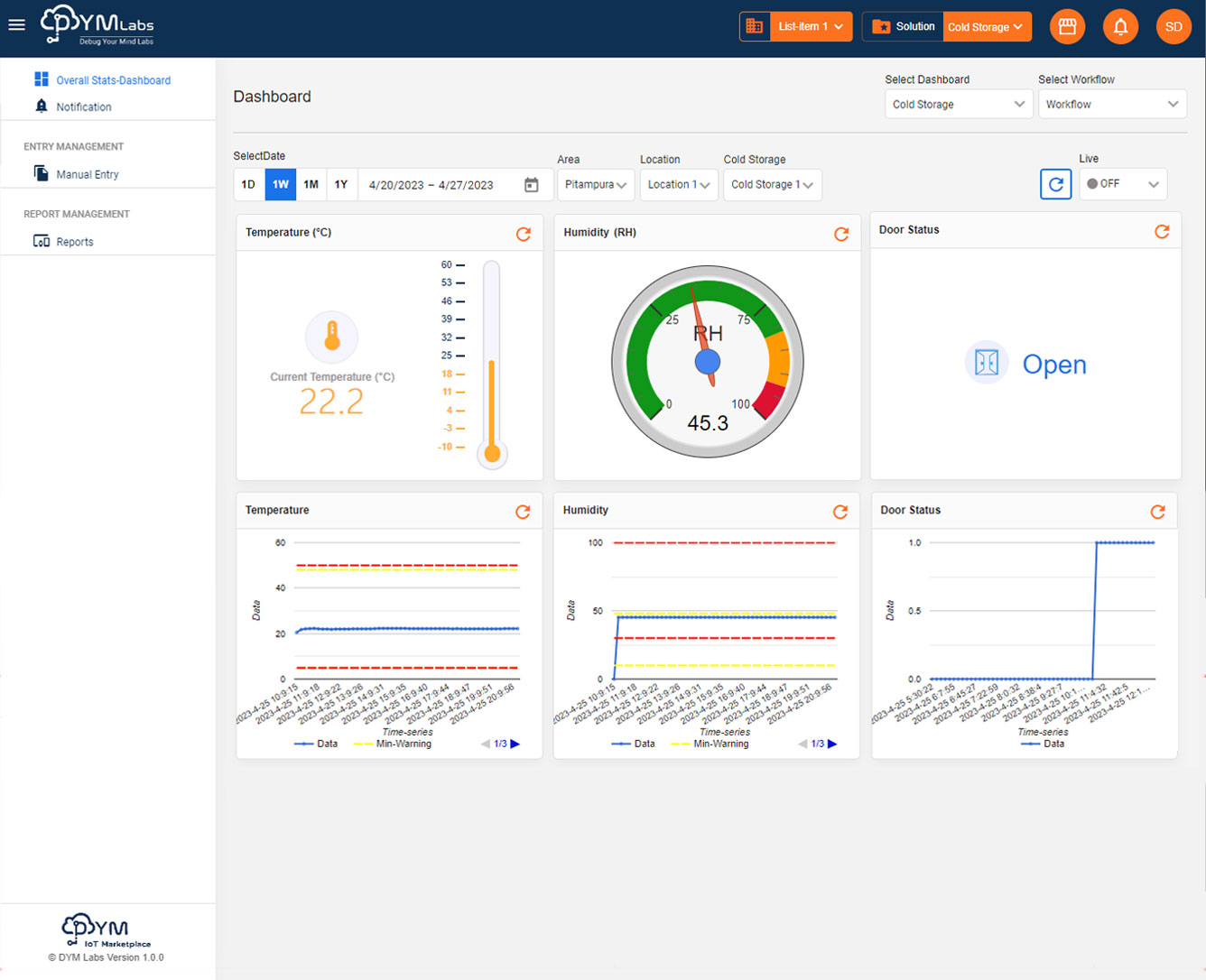
Almost everyone consumes perishable goods daily. Fruits, vegetables, dairy goods, meat and poultry, fresh and frozen foods, fish, and even pharmaceuticals are among these products.
For example, milk typically moves from the cows via pipes connected to cooling storage tanks, also located on the farm and that is where the cold chain begins. Milk remains in the storage tanks, where it’s kept at below 40 degrees Fahrenheit for no more than 48 hours. Tanker trucks pick up and transport the milk to a dairy processor, where it’s tested to ensure it has been properly chilled, and is free of bacteria. Any milk that fails is discarded. Milk theft, the spread of disease, and mistrust between farmers and insurance companies are a few of the issues that this industry is grappled with. Transporting millions of litres of milk every day is not an easy feat. Fresh milk is collected from the dairy farm and then driven to a local dairy processing plant in an insulated, sealed tanker truck. These insulated trucks keep the milk at the optimal temperature throughout the journey. Chilled trucks are used to transport processed Dairy products such as Paneer, Cheese, Butter, etc.
Advent of comprehensive technology offers temperature monitoring solutions to keep your milk at an optimal temperature as well as help to prevent the theft from happening ahead through robust tracking solutions. There is so much more information that needs to be tracked and analyzed than just temperature. Cold chain requires a 360-degree approach to Fleet Management; some of which include: fuel monitoring, load monitoring, On-Board diagnostics, live tracking, dashboards for detailed analysis and RFID/Biometrics.
Ensuring that a shipment will remain within the temperature range for an extended period depends mainly on the type of container used and the refrigeration method.
Cargo refrigeration takes up approximately 20% of all energy consumed in cold chain logistics.
Other factors such as duration of transit, the size of the shipment, and the ambient or outside temperatures experienced are essential in deciding what type of packaging is required and the related level of energy consumption.
In addition to merely wanting to provide consumers with the safest, highest-quality product possible, sectors like food and pharmaceuticals must use cold chain monitoring and data logging from manufacturing onward to comply with federal requirements.
The tricky part about such perishable goods is that they have to be taken special care of. This is simply because if they do not reach on time, they risk expiry, and at the very least, loss of quality. And it’s not about just time, for them to be transported without damage, special measures need to be taken that ensure a safe environment and passage for such goods.
It is crucial to guarantee their safety, quality and make sure that the room's temperature never rises above the ideal level. Many industries have been dependent on temperature-controlled conditions to maintain the quality of their perishable products for which they have been using cold storage facilities for decades. But with global shortages affecting every aspect of the supply chain, these facilities are more in demand than ever. Monitoring these facilities is not an easy task, but the emergence of new technologies has made it quite convenient. What are the common challenges faced by a cold storage owner?
Energy Wastage: Optimising energy usage and monitoring refrigeration equipment in cold storage facilities has become increasingly important to warehouse managers. Energy costs typically account for 15% or more of a warehouse's operating budget, and the lack of data on how much you are being charged for energy doesn’t help either.
Compressor and equipment health: Constantly being concerned about equipment breaking down, compressor health or unintentionally producing significant demand increases becomes time-consuming and challenging.
Maintaining ideal conditions: Precise temperatures, pressure, and humidity for refrigerators and cold rooms’ information, wherever you are, to ensure your settings are within acceptable limits. The need for perfect conditions throughout your whole business, so that the employees can focus less on monitoring and more on the things that matter.
Lack of real-time monitoring: Not getting notified of the temperature fluctuations and power outages, can lead to asset loss or audit failures.
Stock management: Ensuring that all empty spaces are filled with stock as much as possible can take a lot of resources and time which otherwise could have been better utilized.
In our multiple interactions with cold storage owners/managers and after some site visits, we got to see what are the pain points in cold storage, from lack of real-time monitoring to lack of equipment maintenance, from human errors due to lack of digitization to microbial growth and many more…
To counter these issues, DYM Labs has created an IoT-based cold storage monitoring system tailored to the product which leads to the optimum utilization of space and resources. It helps you track the usage pattern and power consumption of devices, minimize wastage, detect anomalies within the facility, and monitor and control the intensity of light as per the changes in daylight. An IoT-enabled monitoring solution that brings terrific value to businesses and enhances profitability.
Some of the benefits that cold storage owners will experience after the implementation of our no-code IoT platform are –
Energy Efficiency: Overall energy expenditures can be decreased with precise temp adjustments to maintain stringent temp ranges (especially for products in different zones in the warehouse).
Real-time monitoring: Monitoring key parameters in real-time identifies variances when they change from their pre-set values; correcting these immediately minimizes product losses.
Stock management: Our cold storage management system informs managers where the empty spaces are within a cold storage warehouse for more effective stocking of products, thereby increasing capacity and throughput.
Audit trails: Our CSM captures data on storage, and analytics provides the documentation required to satisfy regulatory audits, and customer questions, or to expedite recall investigations, if needed.
Product quality: Temperatures are monitored and adjusted as needed in real-time, which greatly improves the quality, safety, and longevity of refrigerated products.
The journey of million miles starts with a single step and by leveraging our IoT-enabled monitoring solution, you will be able to overcome the loss of perishable commodities in cold storage through real-time monitoring. Remote monitoring solutions will further improve the maintenance efficiency of probes and sensors whenever the value from the device deviates beyond acceptable limits. The data that is gathered over time will assist in identifying the ideal storage conditions and the distribution of temperature inside the cold storage facility. This will make it easier for facility managers to locate the hot and cold spots in a cold storage facility and ensure that perishable goods are stored in a way that will preserve their quality throughout a long-term supply of goods. One can see how many invaluable insights are opened to us from data gained which opens multiple dimensions like monitoring energy theft, achieving carbon emission monitoring, and many more.
All in all, it enables the business owner to ensure that everything is ideal throughout their cold storage so that staff can concentrate less on monitoring and more on important items. Our Cold Storage Monitoring solution will send an alert whenever sensors identify substantial temperature, humidity, power swings, and many KPIs with real-time monitoring of numerous points. To know more about how IoT-enabled cold storage monitoring helps to increase your ROI, please talk to our experts.